1955 Mercedes 300SLR Uhlenhaut Coupe
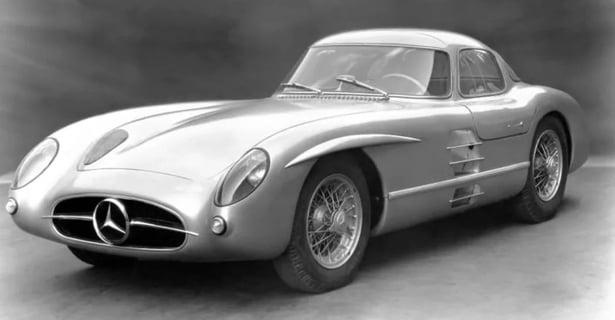
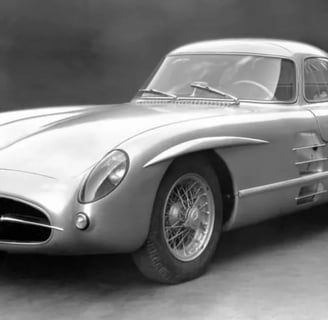
This project is a re-creation of the famous 300SLR Mercedes Race Car. Currently the body is being hand formed is So Africa by Barry of the "Metal Shaping Studio". Barry also is building the tube chassis. The Client enlisted Art Morrison to build the front and rear suspension in a "sub-frame" configuration that will bolt to the tube frame chassis.
The following is a brief description of the actual 300SLR's
The 300 SLR Uhlenhaut Coupe (W 196 S) is considered the first Hypercar in the world. It’s a street legal (!) racecar, weighing only 998 kg. It´s powered by a 3 litre inline-8 pushing 302 hp which makes it capable of reaching speeds up to 300 km/h - in 1955. The fastest street legal production car at the time was the Mercedes-Benz 300 SL with 215 hp and a top speed of 250 km/h.
There are only two original 300 SLR Uhlenhaut Coupes in the world. The one with the red interior was sold in 2022 by Mercedes-Benz for a good cause: To fund scholarships for students. It’s called the beVisioneers program, the link is in our bio. The car achieved the record price of €135 million ($142 million), making it the most expensive car to ever be sold. The second 300 SLR Uhlenhaut Coupe (blue interior) still belongs to Mercedes-Benz and resides in our Museum.
SLR is short for Sport, Leicht, Rennen (Sport, Lightweight, Race).
The nickname “Uhlenhaut Coupe” revers to Rudolf Uhlenhaut. He was the head of the Mercedes-Benz racing division at the time and used the coupes as his company cars on public roads, covering the 220 km between Stuttgart and Munich in roughly one hour. (Radar speed checks in Germany were first introduced in 1959.)
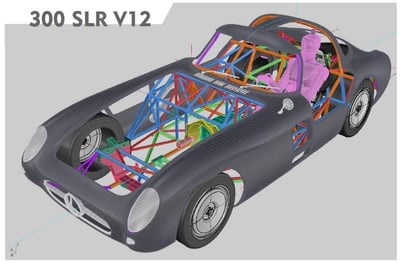
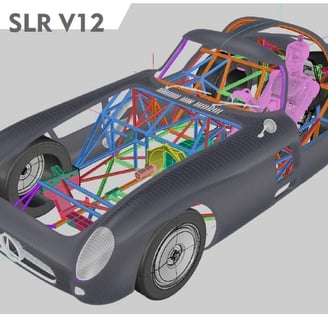
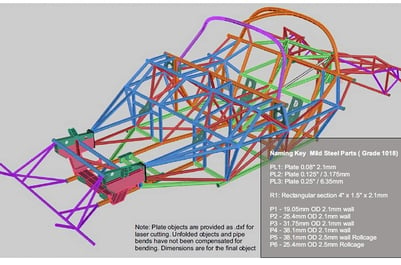
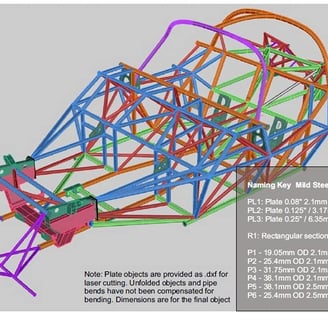
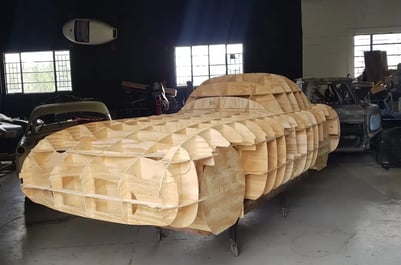
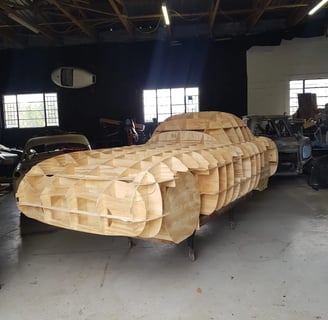
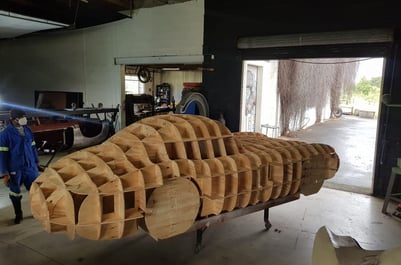
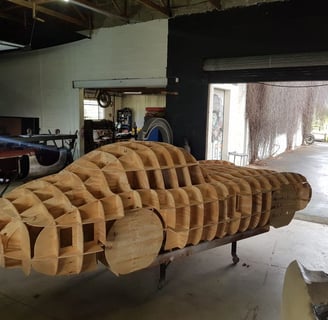
Our project started as a 3D cad drawing by Kevin at "Car Body Bucks". Kevin build a human figure the resemble the size of the client so the car could be modified to fit him comfortably, which stretched the car a bit, and made it a bit taller and wider. The whole tube frame had individually labeled tubes for a complete cut list.
When the design was finalized, Kevin cut the plywood for the "Buck" which is used to form the aluminum skin over. The delivered it to Barry. Several areas of the buck are removable so the these sections can be formed separately, like the windshield.
And then the metal work begins, English wheels, power hammers, hammer and dollies.
And after most of the panels are formed and welded together, the whole body is fastened tot he chassis and all the interior panels can start taking shape, doors, boot and bonnets are formed and hinged.
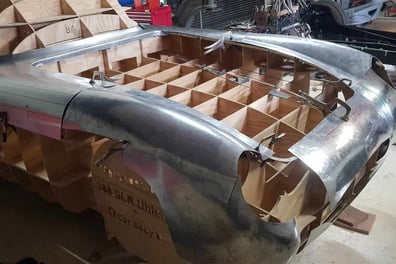
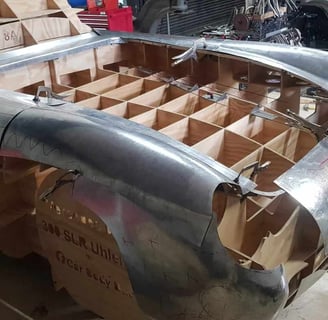
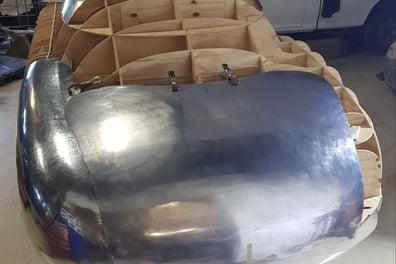
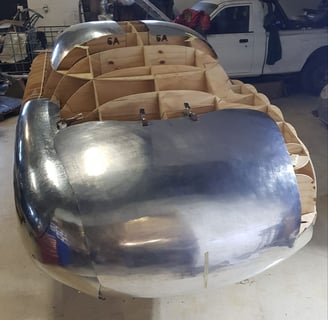
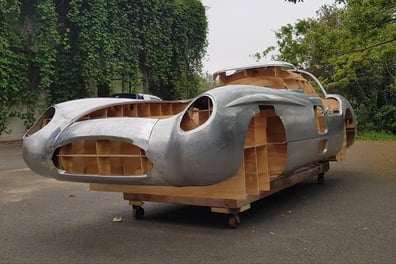
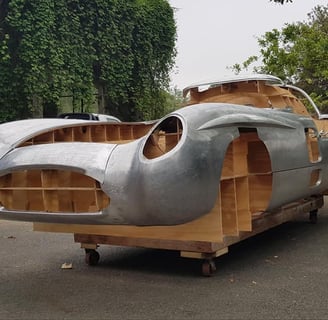
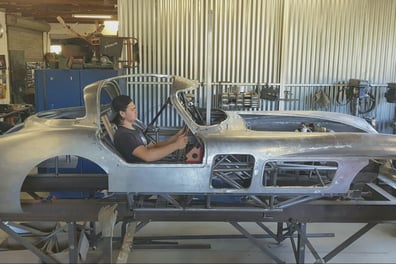
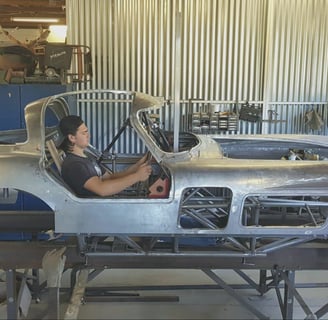